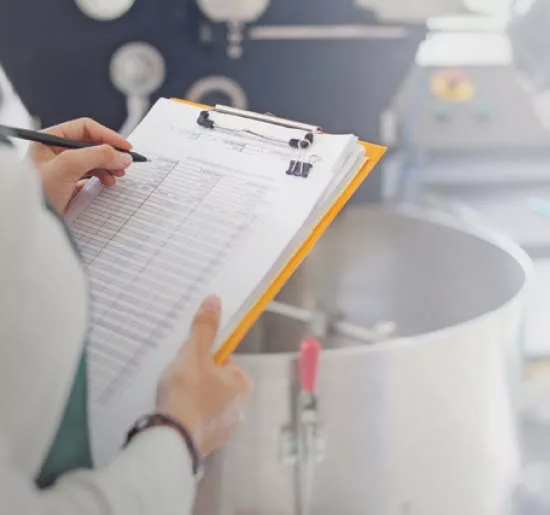
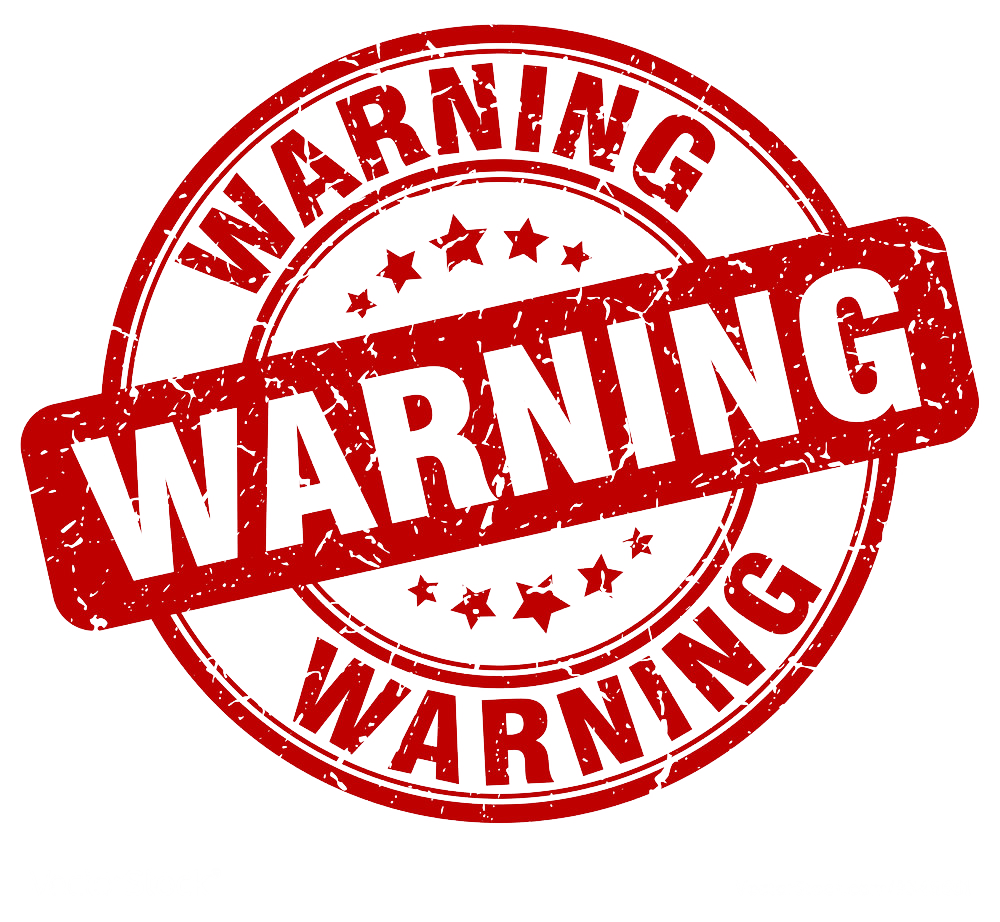
Proactive remediation is in response to an identified risk or possible process breakdown as part of a Continuous Improvement Program. To identify major issues before they occur, proactive remediation requires quality system gap assessments, monitoring of KPIs and quality metrics, and process and management reviews. Being proactive about problems and having remediation processes in place is less costly and requires less time and resources.
FDA Form 483 or warning letter, customer audit, product recall, manufacturing process failure, ineffective standard operating procedures, or backs logs of investigations and complaints. Starting the remediation process as a reaction to a problem is costly, time consuming, and requires many resources.
When developing a Continuous Improvement Program, the first step should be identifying shipping process risks or failures and what improvements could be made to reduce those risks. A CI program should also establish procedures for monitoring processes (KPIs, Quality Metrics, Performance Metrics, etc.) for improvement and risk prevention. Lastly, a CI program should include standards for skilled resources and for cross training for all third-party personnel.
Incremental improvements are small changes over time to improve a method or practice. These small changes are typically low-cost and low risk. An example of incremental improvements would be transitioning a paper record system to electronic record management or updating standard operating procedures and work instructions regularly. Many of these activities are considered forms of remediation.
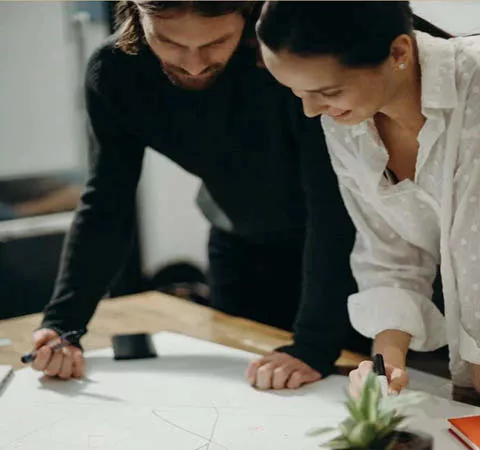


Going through the cycle is a continuous process. Results and solutions must continuously be monitored for potential problems and solutions. Each step of this process involves various types of remediation, such as monitoring, gap analysis, and making changes. Using continuous improvement in conjunction with foundational remediation principles will help to keep GmP systems proactive, rather than falling victim to reactionary remediation.

It was assumed that the root cause of this issue was temperature variations in the cargo hold of the aircraft during shipment. New carriers were utilized, and some existing carriers were eliminated from the process This did not reduce the influx of temperature excursions and investigations became “business as usual” at a very high cost.
After management contracted a third party to conduct an objective risk-based assessment of the shipping process, they identified the actual root cause as improper handling of product during layovers and transfers – not in the cargo holds of planes.
By identifying the actual problem, improvements were made to shipping containers, shipping methods, and procedures. This also resulted in updating Service Agreements, usage of multiple Third-Party Logistics providers (3PLs), as well as training for 3PLs to comply with the client’s product handling SOPs. Monitoring of shipments during transit.
This issue could have been avoided if the process had been part of a Continuous Improvement Program to proactively remediate the shipping process and address all possible shipping risks.
Proactive remediation planning requires a qualified team to develop a CI program and understand what expertise is necessary. A process improvement plan should contain proper root cause analysis and risk assessments to prepare for expected outcomes. The plan should also include inputs for processes such as pack-outs, training of handlers, Time Out of Refrigeration (TOR) limits, and 3PL performance.
Jim Darnell is a Quality and Compliance subject matter expert for the pharmaceutical, biotechnology, and medical device industries. Jim has provided guidance with regulatory audit preparation and post audit corrective action plans and his experience extends globally. He has experience in management of Quality Systems including development and remediation. His experience includes working with clinical through commercial Quality Systems.
Jim has served as Chair and Co-chair for FDANews conferences and has authored and delivered online cGMP training courses.

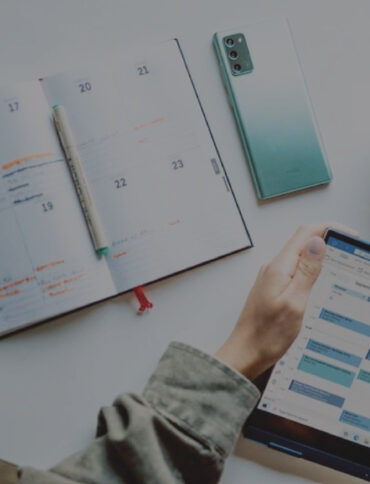
Tips For Preparing & Hosting a Successful Audit
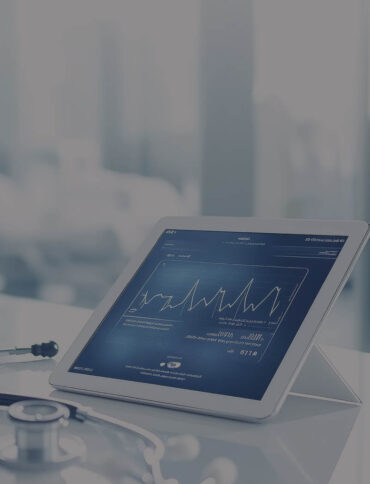
Regulating AI in Clinical Trials: What ICH E6(R3) Does (and Doesn’t) Say
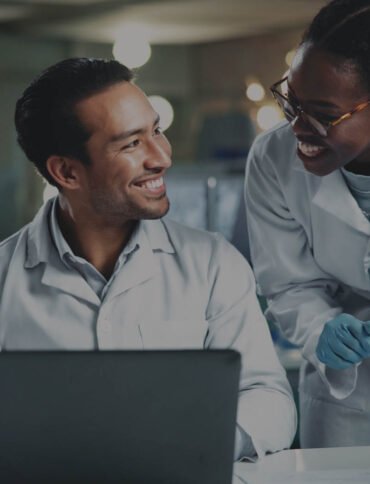
Explores the Differences Between Auditors and Inspectors in the Clinical Research Industry
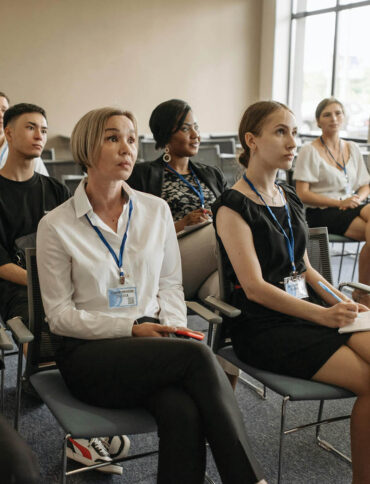
Competency Based Programs Contribute to Early Clinical Research Professional’s Training
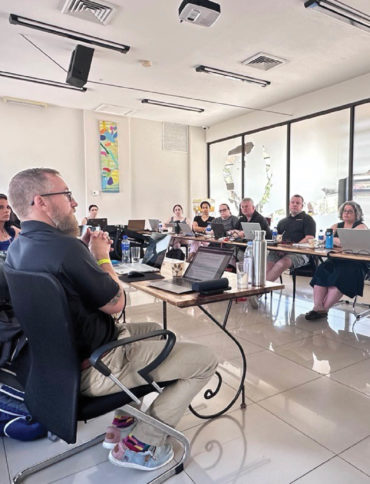
15 Years of Excellence: FDAQRC's Journey and Future Vision
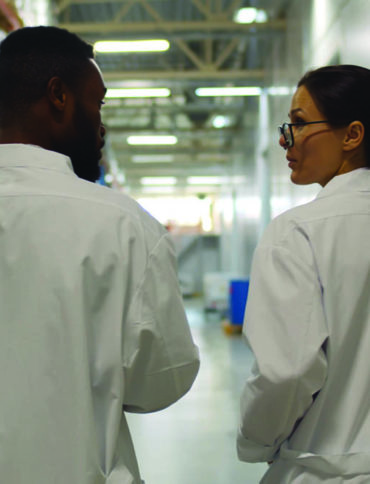
Tips for a Positive Outcome While Performing a Challenging Audit
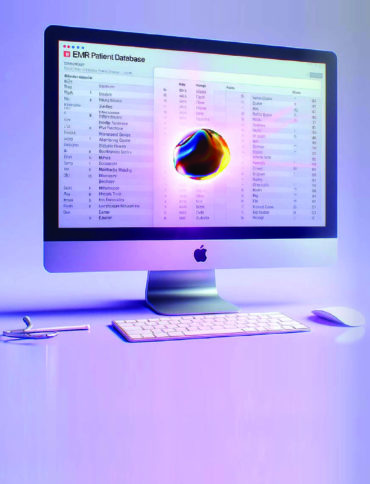
How To Find Qualified Patients for Your Clinical Trials
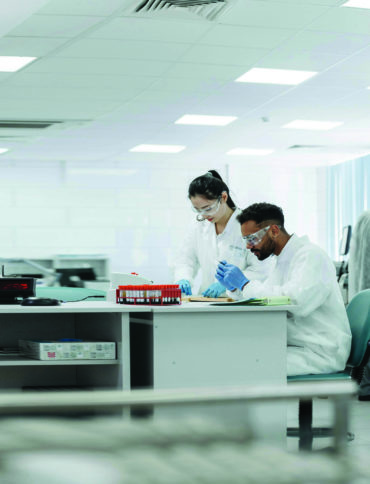