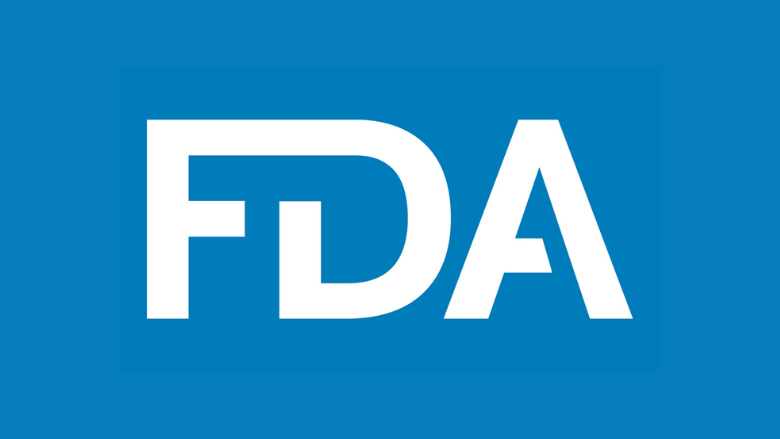
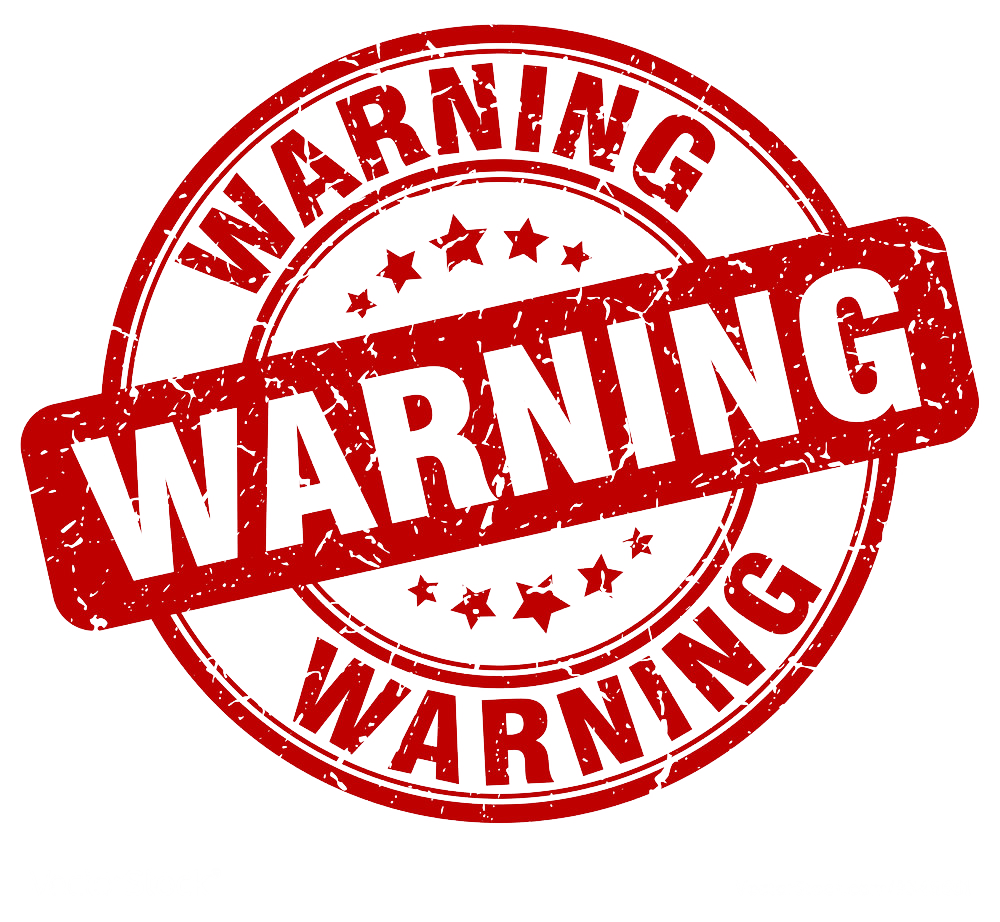
Companies commonly provide employees with SOPs and require them to read and prove their understanding of the training. SOPs and trainings are often assigned in bulk to ensure employees are compliant in an efficient time frame. However, this can lead to employees rushing through documents or skimming through vital information.
Good Manufacturing/Clinical/Distribution Practices (GxPs) require project personnel to be knowledgeable and well trained to ensure the project is in compliance. Compliance culture requires an active understanding of the SOPs from management all the way to operators and technicians. Simply assigning SOPs en masse and requiring a short quiz may not be the best way of integrating trainings.
It has become common for SOP documents to be 20 to 25 pages long. This practice helps in the auditing and inspection process, but not for employee training and project management. Additionally, some SOPs reference multiple procedures or processes in a single document which can cause readers to become lost. To mitigate confusion or regulatory mistakes, simplifying SOPs helps employees have better comprehension and a document to reference as needed. Creating SOPs that are straightforward and easily understandable results in better quality and regulatory compliance.
GxP regulations require instructions and procedures to be followed. However, there is no length restriction or requirement on SOPs and other procedural documents. A company with compliance culture at its core should consider length when writing SOPs. Typically, when an SOP isn’t being followed, it is often because employees struggle to recall the information or find answers within a dense and complex document. This results in employees remembering the document’s complexity rather than its content. In contrast, simple and direct SOPs enhance content retention among employees. It also allows employees to easily refer back to the correct document to ensure they are following the right steps rather than improvising or trying to remember.
In conclusion, effective SOPs are the backbone of regulatory compliance and operational excellence. However, their complexity often hinders their efficacy. Management and SOP authors must prioritize the audience—employees who rely on these documents for guidance. By hiring FDAQRC to review SOPs, companies can ensure these documents are clear, concise, and actionable for all employees.
Gilbert is a former Chemist/Compliance officer with over 20 years of professional experience encompassing complex applications of chemical knowledge and behaviors. He has a strong ability to create and lead across functional teams in company policies, government regulations, and assuring manufacturing sites and clinics are in compliance with all registered pharmacopeias and current regulations.

This Industry Insight was published in July 2024. Please note that the accuracy or completeness of the information contained in this article is based on its publication date, as facts and circumstances may change over time. Please contact us directly if you would like a list of references for this information.
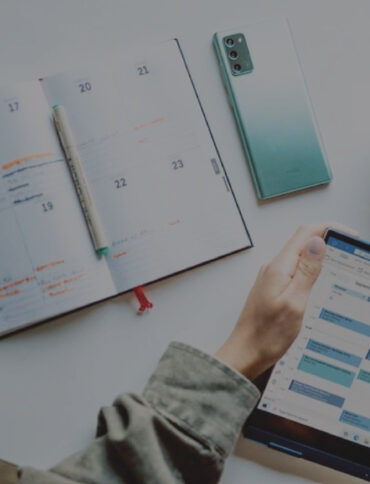
Tips For Preparing & Hosting a Successful Audit
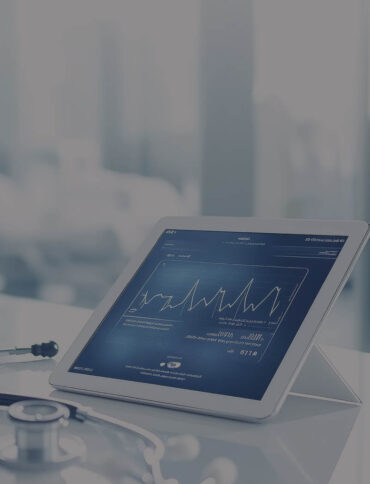
Regulating AI in Clinical Trials: What ICH E6(R3) Does (and Doesn’t) Say
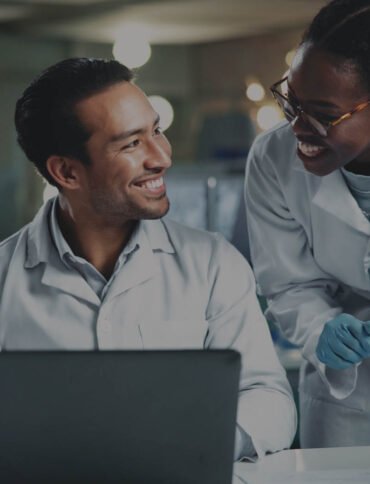
Explores the Differences Between Auditors and Inspectors in the Clinical Research Industry
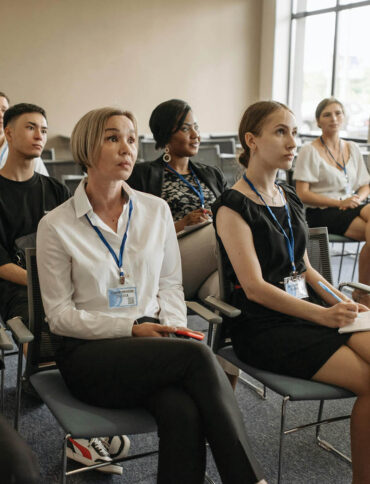
Competency Based Programs Contribute to Early Clinical Research Professional’s Training
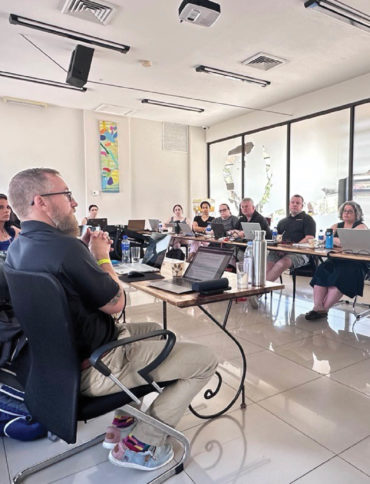
15 Years of Excellence: FDAQRC's Journey and Future Vision
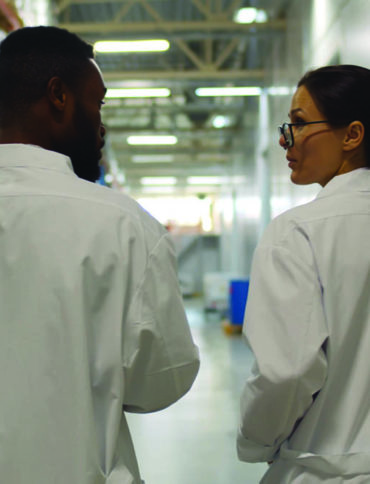
Tips for a Positive Outcome While Performing a Challenging Audit
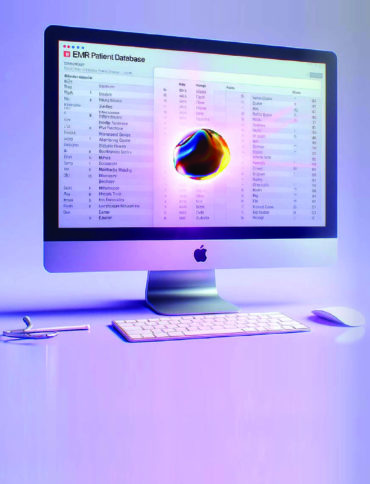
How To Find Qualified Patients for Your Clinical Trials
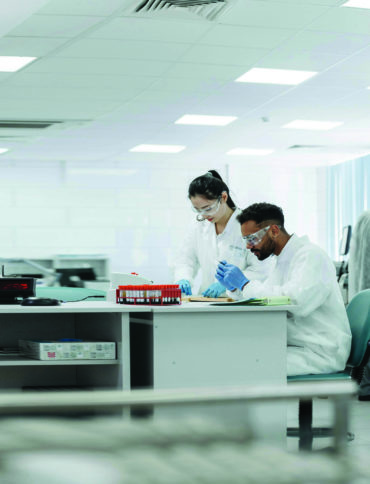